Case Study –Deepwater Disaster Rescue
SEALS 5000 FEET UNDERWATER
April 20, 2010 marked one of the worst environmental disasters in history, the British Petroleum Deepwater Horizon oil rig explosion and spill. RT Dygert was one of the select companies called upon to apply their unique expertise and capabilities in capping this massive leak, estimated to have totaled 4.9 million barrels (or 210 million gallons).
The rig was drilling a 35,000 foot deep exploratory well when high-pressure methane gas expanded into the drilling riser, rose into the drilling rig and exploded with a fire that engulfed the platform. The rig sank to over 5000 feet under the ocean surface, where the failed blowout preventer (BOP) spewed oil that eventually spread over 68,000 square miles. BP was unable to close the blowout preventer valve with remote underwater vehicles, and later with a containment dome.
The oil flow had to be stopped by capping off the damaged blowout preventer. This first required shearing off the damaged components with massive shears capable of working in a water pressure environment with over 10,000 PSI. Likewise, the shears needed to have custom seals that could also operate in these extreme conditions. That’s when RT Dygert was called in to solve these complex sealing problems and help end the disastrous flow of oil.
RT Dygert’s recommendation had to address the following issues.
- Create a comprehensive application data sheet that factored in salt water, oil, extreme pressure, the shear’s size, the weight on the seal, the duration of the operation and more.
- Design a custom seal package, including rod seal, wiper, buffer seal, wear guides and piston seals.
- Seal the hydraulic presses within the custom giant shear by incorporating a buffer seal to handle the pressure spikes; a dual lip rod seal that would not extrude at high pressure and operate at extreme cold temperatures; along with a positive wiper that would not allow salt water to enter the system.
- Design a custom wiper seal to keep the ocean water from entering the cylinder. This seal had to not only prevent contamination from entering the system but also act as a barrier against the sea water entering the system. This is not a simple task at 5000 feet under water where the external pressure is nearly 2500 PSI. Therefore, special consideration had to be given for a wiper that would not extrude in one direction and stay positively loaded to keep ocean elements from contaminating the medium used to power the shear.
- Create design and material specifications for custom seals, accounting for such considerations as pressure, temperature, environment, velocity and medium. However, due to the critical nature of this disaster RT Dygert also had to acquire all seals in a timely manner. This added another challenge to factor in when proposing a solution.
The seals worked to perfection and the shears flawlessly removed the damaged parts so the blowout preventer could be recapped. But, it’s one job RT Dygert hopes will never be needed again.
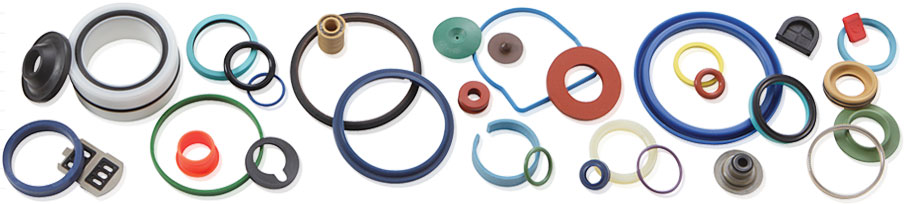