Case Study - RT Dygert Compound N-7045
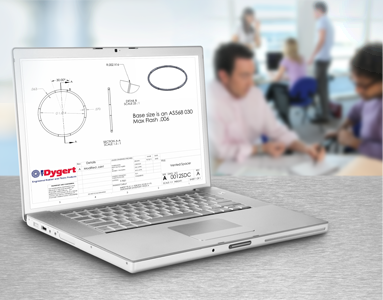
A SAVINGS IN COST AND EFFICIENCY
A long time customer was using a Teflon coated O-Ring as a cap seal on an oil filler tube for a small gasoline engine. Annual usage was 5,000,000+. The use of Teflon was necessitated due to the extremely tight fit of the cap on the filler tube, which made removing the cap very difficult. Modifying the plastic tooling was cost prohibitive, and the customer’s engineering department didn’t want to specify a non-standard O-Ring. An added benefit was, that since the O-Ring was Teflon coated bright blue, it was easy to be sure that the O-Ring had actually been installed, as the color of the cap was black.
However, the Teflon coating created a multitude of problems:
- Due to environmental considerations, the coating had to be done by an outside subcontractor, over which we had little control. Freight and extra handling costs eroded most of our margin on this part. Logistics complicated matters, causing frequent air freight charges.
- The coating process itself is almost “random”. There was no cost-effective, precise way to control the amount of Teflon that was sprayed on the parts. Customer frequently complained of inconsistent “lubricity”.
- Sometimes the coater would forget to post cure the parts, causing flaking or peeling of the Teflon from the O-Ring out in the field. Thus, RT Dygert absorbed several five-figure rework charges. As a result, we decided to post cure the parts after they came back from the coater, to assure that this step hadn’t been missed.
- Four inspections were required on this part: 1) normal incoming, 2) before sending to coater to assure parts had no mold release or anything else on the surface that would inhibit adhesion of the coating, 3) after parts returned from the coater, and 4) after in-house post curing.
- Several safety concerns were raised after discovering that 1) the coating contained a small amount of formaldehyde and 2) workers who handled the parts and then smoked sometimes became nauseous, probably due to the transfer of Teflon from the worker’s fingers to the cigarette, which was then inhaled.
RT Dygert’s solution to these problems was to develop an internally lubricated, blue rubber compound that still met the customer’s material specification. By doing so, we achieved these results:
- Color and lubricity were now tightly controlled, as this was done in the mixing process, before the parts were manufactured
- Lead times were shortened, so RT Dygert was able to reduce the amount of “safety stock” that it was holding in the warehouse.
- Customer experienced no reduced throughput in their automated assembly equipment when compound was changed. Downtime to clean the tracks of the feeder bowls was greatly reduced.
- Field failures were eliminated, as no secondary coating process was now required. As a result, there were no further rework charges.
- Safety concerns were also eliminated. The internal lubricant meets FDA guidelines for ingredients in rubber products.
- Inspections were reduced from four to one. The in-house post curing process was also eliminated.
- RT Dygert’s profit margins were restored, after granting a 12% price reduction to the customer.
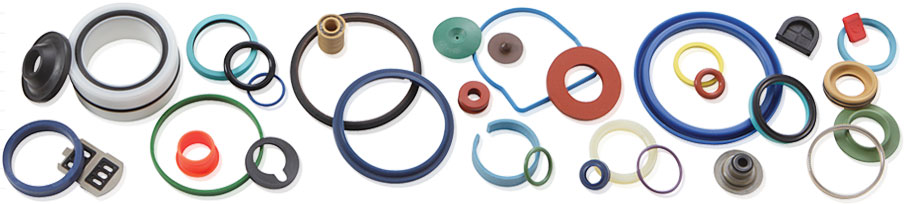